

Furthermore, to demonstrate the effectiveness of the proposed method for determining electric motor specifications, a case study is done for Nordhavn 52 ship. To prove the concept of the proposed topology, confirm manufacturability, and substantiate validity of three-dimensional (3-D) FEM simulations, a small-scale prototype is fabricated and tested.
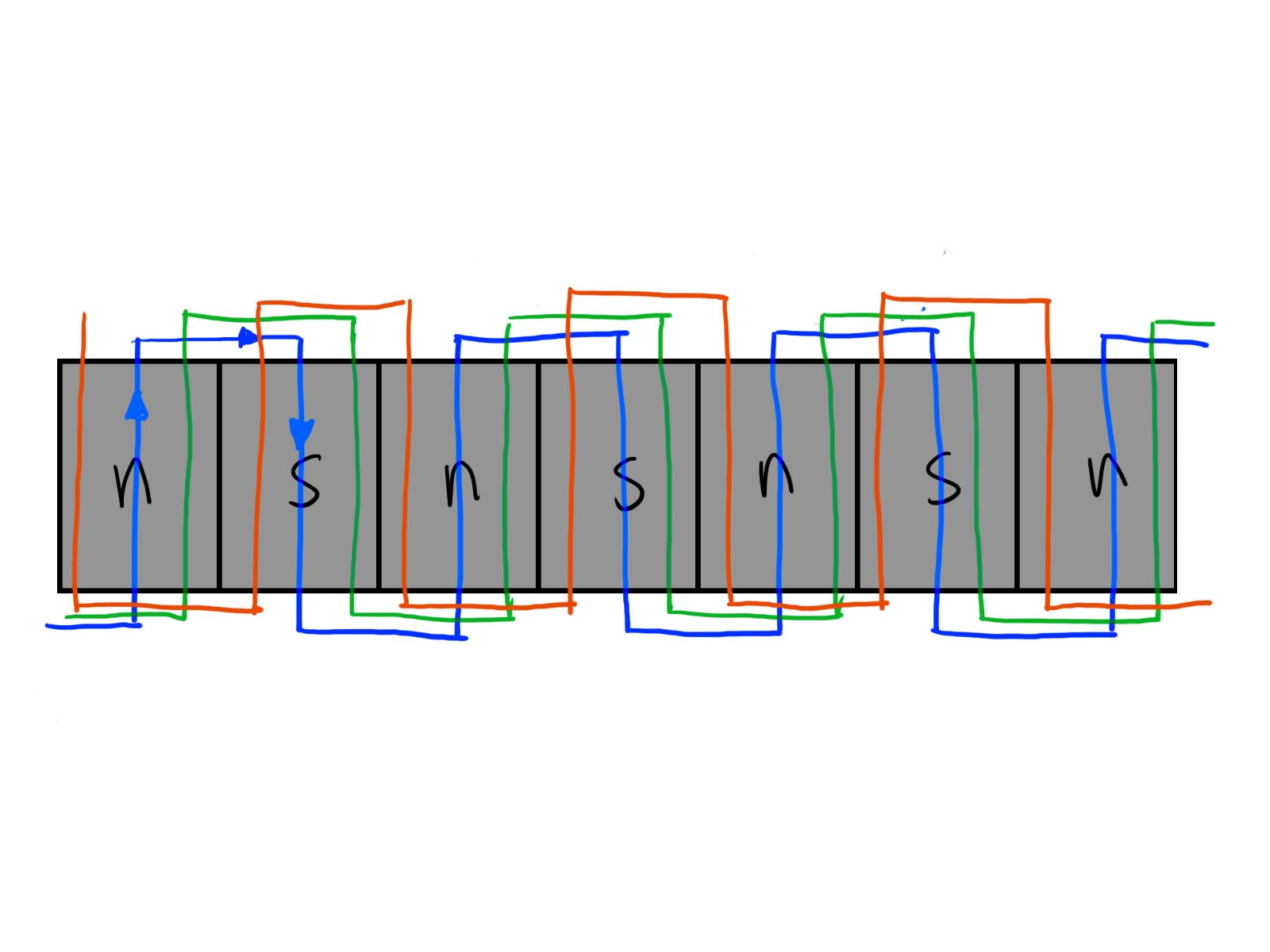
This paper reviews the progress of AFPM technology that has been made in recent years, especially for electric vehicle (EV) propulsions, with respect to the potential AFPM topologies, design. Design methodology and constraints are presented for the ring-winding AFM as well. Axial-flux (AF) permanent-magnet (PM) (AFPM) machine is a competent candidate for electric propulsion applications owing to its high power density, high efficiency and effective volume utilization. The design of its mechanical structure aims to eliminate any unnecessary space. This paper presents a miniature axial-flux spindle motor with a rhomboidal printed circuit board (PCB) winding. This paper presents a new method to determine electric motor specifications considering propeller and hull. Size reduction has become one of the most important aspects of motor design. Due to this integration, the electric motor design is more affected by the design of propeller and hull. In rim-driven thruster, the electric motor is fitted in the duct surrounding propeller so that electric motor and propeller are integrated into one unit. Ring-winding AFM has many advantages, such as reliability, simple construction, ease of increasing phase numbers, and pole numbers, which are important for marine application. This paper proposes an application of a new electric motor topology named ring-winding axial flux machine (AFM) for rim-driven thruster of ship propulsion system.
